Why Spray Balls are the worst choice in tank cleaning
Spray balls were originally designed as a chemical distributing device, relying purely on the amount of chemical, rather than the impact to clean. Today, with rising chemical and water treatment costs and discharge restrictions, quicker CIP cycles are required, using less chemical whilst combining impact cleaning.
Conventional spray balls struggle to achieve this. The design of many spray balls also means that whatever foreign material enters the ball may not be able to escape, acting like a sieve until it blocks, which can lead to wasting a batch, tank cleaning becoming defective until maintenance is carried out, and increased bacteria counts.
There are better tank cleaners than spray ball technology. Even the newest spray balls are poor performers in comparison to rotary head cleaners. The upfront cost of replacing spray balls is quite small, taking into consideration the much higher operation costs of spray balls.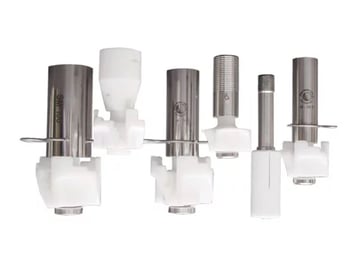
Independent studies of rotary head cleaners have shown dramatic decrease in cleaning cycle times, water consumption, chemical usage, and cleaning effectiveness, when compared to spray ball cleaners.
Spray balls are not only costing businesses, they are also costing the earth. For every litre of water saved, your business contributes to less carbon footprint to our planet. With manufacturing currently experiencing relatively modest growth, literally every second counts.
Production times are dependent on cleaning cycles. If that time can be cut by just 10 seconds, profits can grow dramatically. Rotary head cleaners, such as Gamajet from Alfa Laval, can cut at least 40 seconds of cycle times.
Spray Nozzle Engineering has demonstrated experience in tank cleaning solutions matched with reliable technical and after-sales support. Partnerships with the world leaders in tank cleaning equipment combined with in-house engineering and customisation delivers a product range to cover every tank cleaning, sanitising and wash-down application.