Guidelines for choosing the right spray nozzle for any industrial application
Selecting the right spray nozzle for your application requires lots of understanding and it could become a complex process. Selecting a nozzle that isn't completely suitable for a specific application could increase costs and reduce productivity.
It is important to consider factors such as:
- Spray angles and patterns (coverage to achieve)
- Droplet size (from fine mist to coarse spray)
- Flow rates
- Pressure
- Liquid to be sprayed (viscosity)
Find below more information about factors to consider when selecting spray nozzles for different applications and industries.
How to control dust in the mining industry
Effectiveness of Different Dust Suppression Spraying Devices in Coal Mining
As the coal mining industry worldwide has come under more scrutiny, companies in the field work to keep up with technological advancements. They especially note progress in health, safety, and the environment.
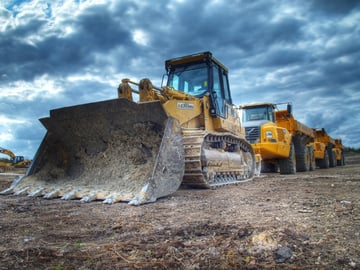
Explosions, cave-ins, and equipment accidents can have tragic consequences while making the
headlines. The pernicious effects of coal dust, however, may have had an even greater impact on illness and deaths over the past century and a half.
To protect the safety of their valuable employees and also to remain compliant with federal health and safety regulations, coal companies realise that they must keep coal dust suppression in the top tier of their safety priorities.
Read more |
Shower nozzle system helps faster nozzle changes
When buying nozzles for pulp and paper making, you may need to evaluate the cost of a nozzle change out, retrofit, or a new installation of spray bars. Selecting the right nozzle can certainly contribute to slow nozzle change outs and impact production.
Paper mill manufacturers require shower nozzles that are easy to use and install, a change out system that could potentially save customers thousands of dollars in time and productivity. Operators should be able to change out multiple nozzles in a fraction of the time of conventional nozzle change out systems by holding ergonomic adjustment tools with just one hand.
Other factors to consider when choosing shower nozzles, is having a system that eliminates incorrect alignment and safety hazards. Nozzles that use locating disc locks, align in the correct orientation every time, due to single direction rotation are a must.
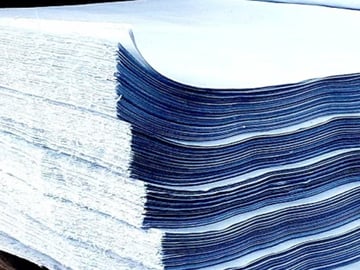
Spray Nozzle Engineering, serving the pulp, packaging, and fibre recycling industries for over 30 years, tackling all the industry concerns addressed above, by manufacturing and supplying the SnapDisc™shower nozzles.
Snap Disc™ nozzle’s secure alignment and quick release mechanism ensure consistent, and rapid change out performance on every spray nozzle. Encompassing a locating disc, flat flan or needle spray disc, gasket and weld base, in a large selection of pipe diameter fittings and seal options, the Snap Disc is the most comprehensive and biggest cost-saving shower nozzle change out system available.
Snap Disc, designed and made by Spray Nozzle Engineering for Australia, New Zealand international paper mills and OEM shower upgrades.
Read more |
Air Atomising Nozzles for Precision Applications
Industries throughout Australia use air atomising nozzles for a variety of applications. Any application that requires a misting spray or a low and steady flow rate works well with this equipment. Coating, glazing and humidifying areas are three popular uses. It’s also not uncommon to see air atomising nozzles used in precision glazing or coating applications like chocolate candy coating or egg glazing.
Understanding Why Air Atomising Nozzles Work for Precision Applications
Air atomising nozzles give a neat and even coating on whatever they spray, especially if the products move through the spray on a conveyor belt at a steady pace. A flat fan spray pattern evenly coats the items as long as the conveyor belt moves at a steady pace. For operations that start and stop, using full cone air spray pattern would provide even coverage for the products.
The XA air atomising nozzle system breaks up the fluid into tiny particles before spraying it using a stream of compressed air. The liquid and air stream mix before exiting the nozzle head in either a full cone or flat fan spray pattern. Air atomising nozzles use low flow rates, and you’re able to set them at a few different angles. All of these factors combine to give uniform coverage and precise control.
The XA 10 and 11 bodies attach to these nozzles. The system allows for up to three cycles per second, and it contains an internal air cylinder that controls the spray’s pressure level. The XA nozzles come with several custom materials that allow you to customise your setup to fit your industry needs. They utilise an on/off operation and work well with standard and specialised application processes.
Read more |
Choosing the right type of nozzle to be used for fire suppression depends on a number of factors. Considerations include the flow rate, the kind of fire and proximity, type of fluid either if its foam, vapour or water, the environment that it’s in as it may bring particles that could block the nozzle; and whether the firefighter at the nozzle or the pump operator has control of the flow or if it’s predetermined.
Optimal vehicle fire nozzles should provide consistent spray distribution and fire suppression performance. They need to be resistant to high heat and dust prone environments, as well as, to produce a uniform distribution of small to medium sized droplets, in both standard and wide angle, full cone spray patterns.
For an optimal foam fire protection in mining, farming, forestry and other applications where nozzle orifices require protection, fire nozzles should not contain rubber or silicone seals, thus avoiding degradation and adhesion problems that can occur with these components.
Ideal design features of fire protection nozzles should include:
- Uniform distribution of droplets in full cone pattern
- Droplet size larger than in hollow cone nozzles of equal capacity
- Small to medium droplet size
- Male & female connections
- One piece body with removable core
- Various core options available
These nozzles should be available in many spray angles and flow rates and a wide selection of materials, thread sizes and industry approvals, including Factory certifications.
Read more |
When deciding what fire protection nozzles to be used for road tunnels and other fixed suppression installations in marine, offshore and in the petroleum field, it’s important to consider factors such as the flow rate, the kind of fire, type of fluid either if its foam, vapour or water, the environment that it’s in, and if someone has control of the flow or if it’s predetermined.
There are five major categories of nozzles for fire protection:
- Solid stream
- Fixed or single flow rate nozzle: This the most simple form of fire nozzle. It provides flow at a predetermined rate that cannot be altered while in use.
- Variable or adjustable flow rate nozzle: This nozzle allows the operator to manually select a desired gallonage while in use.
- Automatic or constant pressure nozzle: Designed to maintain a relatively constant pressure over a wide range of flows.
- Multi-purpose nozzle: This is a mix of solid hollow cone and fog nozzle, providing maximum reach and heat absorption. This nozzle can be well suited for multiple applications including indoors, outdoors, high-rise, Compressed Air Foam System (CAFS), cooling and ventilation.
Read more |
Many plants and factories in Australia and New Zealand face challenges when outsourcing spraying solutions such as custom spray lances, injection quills, and chemical injectors.
It’s time consuming and requires lots of project management to source pipe, flanges, nozzles, and fittings separately; then coordinate fabrication and test procedures of the assembly.
By consolidating into a single engineering supplier, plant managers can trust their lances will be correct the first time, every time.
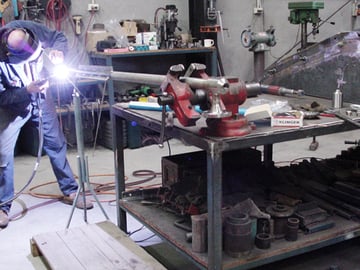
Full-service engineering companies that specialise in spraying nozzles and custom solutions, such as Spray Nozzle Engineering, facilitate the process of getting custom spray nozzle lances installed in Australia and New Zealand plants. These type of companies can also provide the piping section into which lances are installed and everything needed from the concept design stage to on-site delivery; right down to the gaskets, studs, and nuts.
There are many benefits to single-sourcing all components related to spray lances. This ensures that there are no last minute on-site surprises, and customers can concentrate on larger process details knowing that the outsourced engineers are working for them.
However, choosing a full-service engineering company to do this type of job is not enough.
Read more |
A retractable lance allows you to withdraw your nozzle, isolate it from the process, and then remove it completely for servicing without taking your process offline. Once the nozzle is serviced, cleaned, or inspected; simply reattach it to the system, open the isolation valve, and insert it back into the process. This is often a critical requirement for petrochemical facilities where process outages are costly.
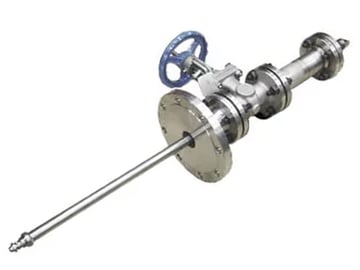
For example, certain applications involved in the production of petroleum contain particles that are very erosive. The ability to remove the nozzle for refit while keeping the process online offers a tremendous cost savings.
Spray Nozzle Engineering, the exclusive supplier of BETE nozzles in Australia and New Zealand, offers a robust retraction mechanism that effortlessly moves the lance from extended to inserted and back. A simple cordless drill is all that is required to power the unit, making this design a favourite with maintenance crews. The mechanism is flexible in its configuration; allowing alternate electric, pneumatic, or hydraulic power sources to drive the unit.
Read more |
Automatic Spray Nozzles for Precision Food Processing and Industrial Applications
Industrial applications require innovative and tailored spray systems to ensure uniformity from product to product. Automatic spray nozzles remove the manual work and the need for manual application from a human worker.
This automation speeds up production times and creates precision consistency that easily meets the high standards set by third-party certifiers. It brings out a host of other benefits as well, and we'll outline them below.
General Benefits and Advantages of Using Automatic Spray Nozzles
Fluid spray nozzles come with several broad-range benefits. These benefits are what makes them so popular for industrial applications and in the food processing industry. They include but are not limited to:
- Comes with high-speed cycling to increase your line speed and boost your output ratios
- High to low flow rate options from a single sprayer tip. These fluid spray nozzles reduce downtime and expenses involved in changing out the tips
- Minimal overspray or misting to improve employee safety
- Optimises performance for the automatic flow control based on your unique operating conditions like speed and volume
- Sprayed solution seamlessly goes to the intended target with minimal waste
- Wide range of automatic spray nozzles available to buy and test
Read more |
Eductor nozzles, also known as jet pumps, venturi pumps or ejectors, are the easiest way to mix, heat or pump different types of liquids, gases and solids either in-line or in-tank in the petrochemical and other industries. Eductor nozzles are also used to:
- Clear sludge
- Prevent sediment
- Liquid draining
- To heat fluids in-line
- Pump in hazardous areas where electric pumps can’t be used
- Create movement in liquid
- Agitate for particle suspension
- Dilution of acid or liquids
- General mixing
- Breaking up a grease layer
- Fire protection water storage tanks
- To inject and mix chlorine, water additives, chemicals, acids, paint, coatings, platings, phosphate, dyes, pulp, fertilisers and slurries.
- To evacuate gases
- To evacuate vessels
- Create a vacuum
- Boost suction pressures
- To scrub fumes from a gas
Read more |